- 20.02.2017
- Источник: Журнал "Нефтегазовая вертикаль"
- Категория: Пресс-центр
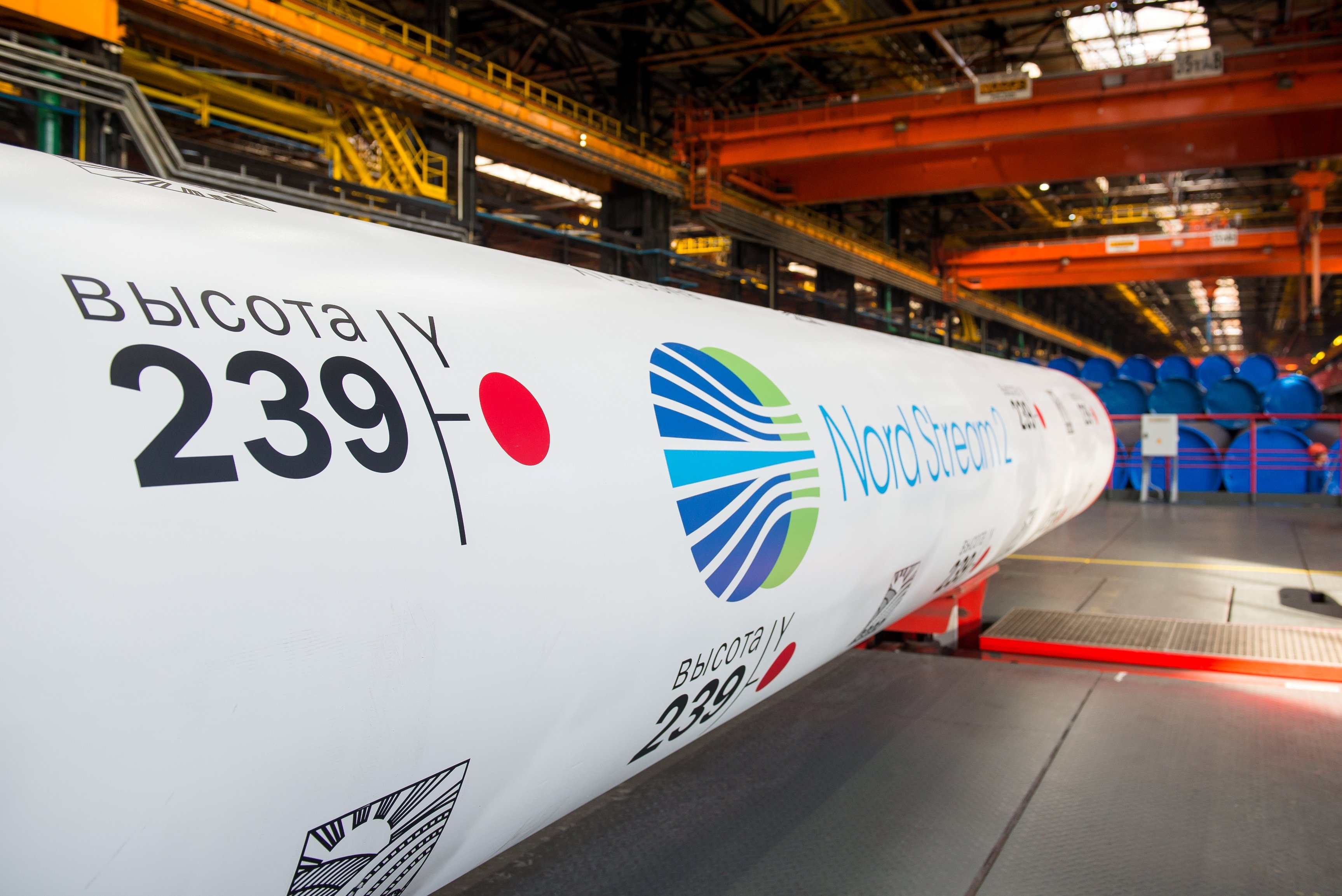
Несмотря на нестабильность конъюнктуры мировых рынков углеводородов, ТЭК по-прежнему нуждается в высокотехнологичной инновационной трубной продукции. Увеличение протяженности нефтегазовых скважин, рост объемов бурения, поддержание добычи на традиционных месторождениях и выход на новые территории с неразвитой инфраструктурой требуют от производителей труб повышения качества и расширения сортамента выпускаемой продукции. В результате масштабного перевооружения отрасли, осуществленного с начала 2000-х годов, доля высокотехнологичной продукции в производстве ведущих отечественных трубных компаний сегодня превышает 60%. В прошлом году головные компании отрасли — ТМК, ЧТПЗ и ОМК — представили новые образцы трубной продукции и ввели в эксплуатацию ряд новых мощностей по выпуску инновационных труб и оборудования. Благодаря достигнутым успехам трубная отрасль уже не нуждается в прямой государственной поддержке. Наоборот, помощь новым проектам приведет лишь к созданию избыточных активов и возникновению трудностей для действующих игроков рынка.
В 2016 году в рамках программ по импортозамещению крупнейшие игроки рынка — ПАО «Трубная металлургическая компания» (ТМК), АО «Объединенная металлургическая компания» (ОМК) и ПАО «Челябинский трубопрокатный завод» (Группа ЧТПЗ) — вложили более 21 млрд рублей в повышение качества и расширение линейки производимых труб. В результате было закрыто практически 100% потребностей компаний ТЭК в высокотехнологичной трубной продукции.
В частности, российские трубники обеспечили спрос «Газпрома» и Nord Stream 2 AG в трубах большого диаметра для проектов «Северный поток-2», «Ухта–Торжок-2» и «Сила Сибири». Для обустройства месторождений был налажен выпуск насосно-компрессорных и обсадных труб, устойчивых к воздействию сероводорода, а также труб, устойчивых к воздействию сверхнизких температур.
Стоит отметить, что технологические успехи трубников достигнуты на фоне общего снижения рынка, прежде всего в сегменте труб большого диаметра.
Премиум-сегмент ТМК
В прошлом году ТМК инвестировала более 10 млрд рублей в комплексную программу по расширению мощностей и повышению качества труб премиального сортамента. Так, были модернизированы линии финишной отделки труб для добычи углеводородов, внедрены современные средства неразрушающего контроля, реконструированы линии по производству ТБД. В результате были улучшены геометрия труб и качество нанесения покрытий.
Компания продолжила также совершенствовать технологии производства премиальных труб с соединениями семейства ТМК UP. Среди этих разработок — трубы размером 114,3х6,88 мм группы прочности L80 13CrS с премиальным резьбовым соединением ТМК UP FМТ и муфты к ним. Их выпуск налажен на Синарском трубном заводе. А передельные трубы и заготовка для муфт производятся на Волжском трубном заводе (оба входят в состав ТМК). В разработке и освоении этой продукции участвовали «Газпром ВНИИГАЗ» и структуры ТМК — научно-исследовательский центр РосНИТИ и предприятие «ТМК-Премиум Сервис».
Выпускаемые ТМК трубы из стали мартенситного класса типа 13Cr, 13CrS, 13CrL («суперхром») обладают повышенной хладостойкостью и коррозионной стойкостью в средах с высоким содержанием диоксида углерода (углекислотная коррозия — наиболее опасный вид разрушения труб и внутрискважинного оборудования).
Хладостойкость сталей класса «суперхром» достигается пониженным содержанием углерода, а также наличием в составе, кроме 13% хрома, никеля (4–6%) и молибдена (1–3%). Эти элементы повышают вязко-пластические свойства стали, в том числе при отрицательных температурах.
В связи со структурной особенностью стали марки 20Х13 (высокое содержание карбидной фазы), применяемой для производства продукции группы прочности L80 тип 13Cr в обычном исполнении, увеличить ее хладостойкость методами термической обработки довольно сложно.
Поэтому РосНИТИ предложил относительно экономную легированную сталь марки 15Х13Н2. От упомянутой стали марки 20Х13 она отличается более низким содержанием углерода и дополнительным легированием никелем в количестве 2%.
Кроме того, в 2016 году ТМК начала производство теплоизолированных лифтовых труб (ТЛТ) в исполнении Light. Они представляют собой сборную конструкцию: труба меньшего диаметра размещена в трубе большего диаметра. Межтрубное пространство заполняется неорганическим волокном для уменьшения теплопотери. Трубы применяются в качестве насосно-компрессорных для обустройства нефтяных скважин в условиях вечной мерзлоты.
Впервые ТЛТ Light были запущены в эксплуатацию во втором полугодии 2016 года на объектах «Тюменнефтегаза» и заслужили доверие заказчика. В результате ТМК была допущена к участию в тендере, по итогам которого получила право на поставку около 80 тыс. метров труб в 2017–2019 годах. Выполнение этого заказа началось в декабре 2016 года.
В прошлом году было отгружено 14,5 тыс. метров ТЛТ Light дочерней структуре «Роснефти» и ее совместному предприятию с «Газпром нефтью» — «Мессояханефтегазу».
Еще одна инновационная разработка ТМК — обсадные трубы класса Премиум с бессмазочным покрытием GreenWell. Покрытие позволяет производить свинчивание резьбовых соединений обсадных и насосно-компрессорных труб без нанесения смазки. Это существенно сокращает время на подготовку труб к спуску и расходы компаний при освоении месторождений, а также минимизирует ущерб окружающей среде. В 2016 году ТМК отгрузила эту продукцию «Газпром нефть шельфу», Statoil и дочерним структурам ЛУКОЙЛа. Трубы предназначались как для морских (Приразломное, Сарматское), так и для сухопутных (Митяевское, Неприковское) месторождений.
В 2015 году ТМК заключила долгосрочное соглашение с «Газпромом», которое предусматривает разработку и производство продукции по специальным техническим условиям концерна. Речь идет о высокопрочных и специальных трубах с премиальными резьбовыми соединениями из углеродистых и легированных марок стали и специальных сплавов для эксплуатации в сложных климатических условиях и агрессивных средах.
В прошлом году в рамках этого договора были разработаны насосно-компрессорные трубы диаметром 89 и 114 мм из сероводородостойкой стали С90SS. Они предназначены для Астраханского месторождения «Газпрома», в продукции которого содержатся сероводород и углекислый газ в высокой концентрации.
Нанотехнологии ЧТПЗ
Инвестиции Группы ЧТПЗ в создание высокотехнологичной продукции в прошлом году составили около 5 млрд рублей. Стимулом для инновационных импортозамещающих разработок здесь также стало сотрудничество с «Газпромом». В 2016 году председатель правления концерна Алексей Миллер и основной акционер Группы ЧТПЗ Андрей Комаров подписали дорожную карту по освоению про-изводства труб нового поколения. В соответствии с документом, трубная компания разработает технологические решения по изготовлению труб большого диаметра и соединительных деталей трубопроводов с использованием лазерной сварки. Этот метод будет впервые в мировой практике применен для серийного изготовления ТБД.
Также в прошлом году ЧТПЗ и «Газпром» приняли программу научно-технического сотрудничества в целях обеспечения перспективных потребностей газового концерна в трубной продукции. В ее рамках предусмотрено взаимодействие по пяти основным направлениям: электросварные трубы большого диаметра, обсадные трубы, насосно-компрессорные трубы, соединительные детали, запорная арматура.
Согласно документу, до конца 2020 года ЧТПЗ проведет более 20 работ по освоению новых технологичных видов продукции. Компания продолжит разработку газогерметичных резьбовых соединений второго и третьего поколений, высокопрочных коррозионно-стойких труб, специальной арматуры и соединительных деталей, устойчивых к воздействию агрессивных сред.
К сегодняшнему дню по заказам «Газпрома» Группа ЧТПЗ разработала ТБД для Южно-Киринского газоконденсатного месторождения, а также трубы большого диаметра с использованием собственного керамического флюса (материала, применяемого при сварке). Флюс производства ЧТПЗ значительно дешевле импортных аналогов и не уступает им по качеству.
В 2016 году металлурги ЧТПЗ также освоили производство новых видов высокогерметичных резьбовых соединений насосно-компрессорных и обсадных труб класса «Премиум», новых марок керамического флюса.
Кроме того, в декабре 2016 года на новом заводе ЭТЕРНО (совместный проект ЧТПЗ и РОСНАНО) при участии президента Владимира Путина запущено производство уникальной для российского рынка продукции — разрезных тройников с использованием нанотехнологий. Технология врезки под давлением на магистральных трубопроводах применяется в России уже около 20 лет.
Но до последнего времени поставку разрезных тройников для отечественного ТЭК и работы по их безостановочной врезке осуществляли зарубежные компании.
Наличие на ЭТЕРНО уникального оборудования и технологий позволило в кратчайшие сроки изготовить опытные образцы и перейти к выпуску промышленных образцов. Среди преимуществ российской продукции — стоимость, скорость производства и доставки (в четыре-восемь раз быстрее по сравнению с зарубежными аналогами), индивидуальность заказа, совместимость с оборудованием для врезки, комплексность поставок.
Разрезные тройники ЭТЕРНО позволяют проводить ремонт магистральных трубопроводов под рабочим давлением до 9,8 МПа и ввод их в эксплуатацию без остановки перекачки углеводородов. Продукция может использоваться в сложнейших природных и климатических условиях.
Ежегодно ЭТЕРНО планирует выпускать до 150 единиц новой продукции под стратегические проекты, такие как вторая нитка продуктопровода Новый Уренгой — Сургут, газопровод «Северный поток-2», обеспечение ремонтно-эксплуатационных нужд «Газпрома», «Роснефти», нефтегазовых компаний стран СНГ.
Запуск новой линейки продукции на ЭТЕРНО эксперты называют шагом к практически полному завершению импортозамещения в производстве магистральных трубопроводов.
Шаровые краны ОМК
ОМК в 2016 году направила 6 млрд рублей на работы по импортозамещению продукции, предназначенной для сложных условий эксплуатации.
В частности, организованы производства по нанесению антикоррозионных покрытий на ТБД, построены мощности по выпуску и отделке обсадных труб со стандартными и премиальными типами соединений, насосно-компрессорных труб, модернизированы муфтонарезные и резьбо-нарезные мощности, запущена новая линия по нанесению антикоррозионных покрытий на соединительные детали трубопроводов.
Но самым масштабным прошлогодним инвестпроектом ОМК стало создание Уральского завода специального арматуростроения (ООО «УЗСА»). Цель проекта — локализация в России производства импортируемых сегодня шаровых кранов специального назначения для газовой отрасли диаметром до 1400 мм, рассчитанных на давление до 42 МПа.
Новое производство налажено на базе промышленной площадки завода «Трубодеталь» в Челябинске (входит в ОМК). Оно включает в себя комплекс высокоточного металлообрабатывающего, контрольно-измерительного и испытательного оборудования, а также мощности для нанесения сверхзвукового газопламенного напыления и другие высокотехнологичные процессы.
Как утверждают в ОМК, новый завод обеспечит современной российской продукцией газовые месторождения с повышенным содержанием агрессивных компонентов, в том числе на шельфе. Кроме того, УЗСА позволит шире использовать при транспортировке газа отечественное оборудование, включая компрессорные станции с повышенными требованиями к надежности и давлениям.
Продукция завода может также применяться при реализации СПГ-проектов и строительстве газоперерабатывающих заводов.
Уже разработанные опытные образцы специальных шаровых кранов ОМК продемонстрировала руководству «Газпрома» на VI Санкт-Петербургском международном газовом форуме в октябре 2016 года. Часть образцов прошла испытания или готовится к ним на объектах концерна.
Освоение выпуска шаровых кранов для специальных условий по полному циклу запланировано на 2018–2019 годы. А в последующие несколько лет будет достигнут максимальный уровень локализации.
Не время почивать на лаврах
«Продолжение активной инвестиционной деятельности крупнейшими трубными компаниями позволяет говорить о том, что они не только успешно выполнили задачу импортозамещения — доля импорта трубной продукции по итогам 2016 года составила 4,5%, — но и перешли к импортоопережению.
Качество и надежность российских труб, как правило, превышают требования мировых стандартов», — отмечает директор Фонда развития трубной промышленности Игорь Малышев.
В масштабное технологическое перевооружение российской трубной отрасли, осуществленное в 2002–2016 годах, было инвестировано более 470 млрд рублей собственных и заемных средств. Благодаря этому, а также текущим инвестиционным проектам доля высокотехнологичной продукции в производстве российских трубных компаний сегодня превышает 60%. Созданных в стране трубных мощностей, прежде всего по производству ТБД, достаточно для удовлетворения текущего и перспективного спроса России и стран ЕАЭС (см. «Лучше без излишеств»).
Между тем нефтегазовый сектор остается широким полем для инноваций трубников. Продолжают расти объемы и глубины бурения, усложняются профили скважин, все более широко применяются горизонтальные и наклонные способы проходки, повышается агрессивность сред. Соответственно, ужесточаются требования к материалам, геометрическим характеристикам и резьбовым соединениям стальных труб для нефтедобычи.
При этом снижение цен на углеводороды, введение западных санкций и ослабление национальной валюты вынудили российские нефтегазовые компании сокращать издержки и искать новых поставщиков оборудования и технологических решений на территории РФ.
Таким образом, ведущим трубным предприятиям страны по-прежнему есть к чему стремиться. Ключевыми направлениями работы отрасли остаются совершенствование труб нефтяного сортамента, а также производство новой трубной продукции для добычи и транспортировки газа в сложных условиях эксплуатации.
Лучше без излишеств
Как отмечают в Фонде развития трубной промышленности, в 2004–2010 годах отечественные компании без всякой господдержки создали современные мощности по выпуску сварных одношовных ТБД. Этих активов достаточно для обеспечения потребности ТЭК, даже с учетом пикового спроса при реализации сразу нескольких крупных магистральных трубопроводных проектов на территории России и ЕАЭС.
В этой связи ФРТП выражает обеспокоенность государственной поддержкой проектов, «создающих новые избыточные мощности в этом сегменте трубного рынка». Такая ситуация, по мнению Фонда, «не приведет к импортозамещению, росту промышленного производства и экономики страны в целом, а только создаст проблемы для действующих предприятий отрасли».
Как считают в ФРТП, среди основных мер, которые бы способствовали дальнейшему развитию трубной отрасли в 2017 году:
- целенаправленная поддержка государством инвестпроектов в сегменте машиностроения;
- реализация крупных инфраструктурных проектов в ТЭК;
- наработка практики правоприменения при использовании б/у труб;
- защита рынка ЕАЭС от недобросовестной конкуренции.
Валентина Анисимова